Teaduse ja tehnoloogia arengu ning majanduse arenguga laieneb lämmastiku kasutusala iga päevaga ning see on tunginud paljudesse tööstussektoritesse ja igapäevaellu.
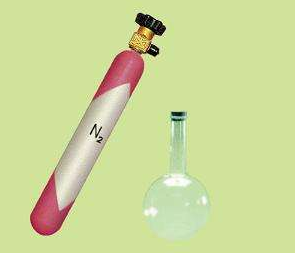
Lämmastikutootmise tootjad – Hiina lämmastiku tootmistehas ja tarnijad (xinfatools.com)
Lämmastik on õhu põhikomponent, moodustades umbes 78% õhust. Elementaarne lämmastik N2 on tavatingimustes värvitu ja lõhnatu gaas. Gaasi tihedus standardolekus on 1,25 g/l. Sulamistemperatuur on -210 ℃ ja keemistemperatuur -196 ℃. Vedel lämmastik on madala temperatuuriga külmutusagens (-196 ℃).
Täna tutvustame mitmeid peamisi meetodeid lämmastiku tootmiseks kodu- ja välismaal.
Üldist tööstuslikku lämmastiku tootmismeetodit on kolm: krüogeense õhueraldusega lämmastiku tootmine, rõhu kõikumisega adsorptsiooniga lämmastiku tootmine ja membraanseparatsiooniga lämmastiku tootmine.
Esiteks: krüogeense õhu eraldamise lämmastiku tootmismeetod
Krüogeense õhueraldusega lämmastiku tootmine on traditsiooniline lämmastiku tootmismeetod, mille ajalugu on peaaegu mitu aastakümmet. See kasutab toorainena õhku, surub selle kokku ja puhastab ning seejärel kasutab soojusvahetust õhu vedelaks vedelaks muutmiseks. Vedel õhk on peamiselt vedela hapniku ja vedela lämmastiku segu. Vedela hapniku ja vedela lämmastiku erinevaid keemispunkte kasutatakse nende eraldamiseks vedela õhu destilleerimisel lämmastiku saamiseks.
Eelised: suur gaasitootmine ja toote lämmastiku kõrge puhtus. Krüogeense lämmastiku tootmine võib toota mitte ainult lämmastikku, vaid ka vedelat lämmastikku, mis vastab vedela lämmastiku protsessinõuetele ja mida saab hoida vedela lämmastiku mahutites. Vahelduva lämmastikukoormuse või õhueraldusseadmete väiksema remondi korral siseneb säilituspaagis olev vedel lämmastik aurustisse ja kuumutatakse ning suunatakse seejärel toote lämmastiku torujuhtmesse, et rahuldada protsessiüksuse lämmastikuvajadust. Krüogeense lämmastiku tootmise töötsükkel (viidates kahe suure kuumutamise vahelisele intervallile) on üldjuhul pikem kui 1 aasta, seega ei loeta krüogeense lämmastiku tootmist üldjuhul ooterežiimiks.
Puudused: Krüogeense lämmastiku tootmisel saab toota lämmastikku puhtusega ≧99,999%, kuid lämmastiku puhtust piiravad lämmastikukoormus, kandikute arv, salve efektiivsus ja hapniku puhtus vedelas õhus ning reguleerimisvahemik on väga väike. Seetõttu on krüogeense lämmastiku tootmisseadmete komplekti toote puhtus põhimõtteliselt kindel ja seda on ebamugav reguleerida. Kuna krüogeenset meetodit rakendatakse äärmiselt madalatel temperatuuridel, peab seadmel enne tavakasutusele panemist olema eeljahutuskäivitusprotsess. Käivitusaeg, st aeg ekspanderi käivitamisest kuni lämmastiku puhtuse nõude saavutamiseni, ei ole üldjuhul lühem kui 12 tundi; enne seadme kapitaalremondi alustamist peab sellel olema kütte- ja sulamisaeg, tavaliselt 24 tundi. Seetõttu ei tohiks krüogeense lämmastiku tootmisseadmeid sageli käivitada ja seisata ning soovitav on töötada pidevalt pikka aega.
Lisaks on krüogeenne protsess keerukas, võtab enda alla suure ala, on suurte infrastruktuurikuludega, nõuab spetsiaalseid hooldusjõude, sellel on palju operaatoreid ja see toodab gaasi aeglaselt (18–24 tundi). See sobib suuremahuliseks tööstuslikuks lämmastiku tootmiseks.
Teiseks: rõhumuutuse adsorptsiooni (PSA) lämmastiku tootmismeetod
Pressure Swing Adsorption (PSA) gaasieraldustehnoloogia on mittekrüogeense gaasieraldustehnoloogia oluline haru. See on inimeste pikaajaliste pingutuste tulemus leida krüogeensest meetodist lihtsam õhueraldusmeetod.
1970. aastatel töötas Lääne-Saksamaa Esseni kaevandusettevõte edukalt välja süsiniku molekulaarsõelad, sillutades teed PSA õhueraldusliku lämmastiku tootmise industrialiseerimisele. Viimase 30 aasta jooksul on see tehnoloogia kiiresti arenenud ja küpsenud. Sellest on saanud krüogeense õhueralduse tugev konkurent väikese ja keskmise suurusega lämmastiku tootmise valdkonnas.
Survekõikumisega adsorptsiooniga lämmastiku tootmisel kasutatakse toorainena õhku ja adsorbendina süsiniku molekulaarsõela. See kasutab süsiniku molekulaarsõela õhus oleva hapniku ja lämmastiku selektiivse adsorptsiooni omadusi ning kasutab rõhu kõikumise adsorptsiooni põhimõtet (rõhu adsorptsioon, rõhu vähendamise desorptsioon ja molekulaarsõela regenereerimine), et eraldada toatemperatuuril lämmastik ja lämmastik.
Võrreldes krüogeense õhueraldusega lämmastiku tootmisega on rõhumuutustega adsorptsiooniga lämmastiku tootmisel olulisi eeliseid: adsorptsiooni eraldamine toimub toatemperatuuril, protsess on lihtne, seadmed on kompaktsed, jalajälg on väike, seda on lihtne käivitada ja peatada, see käivitub kiiresti, gaasi tootmine on kiire (tavaliselt umbes 30 minutit), energiakulu on väike, kasutuskulud madalad, automatiseerituse aste on kõrge, kasutamine ja hooldus on mugav, libisemispaigaldus on mugav, pole spetsiaalset vundamenti on nõutav, saab toote lämmastiku puhtust teatud vahemikus reguleerida ja lämmastiku tootmine on ≤3000 Nm3/h. Seetõttu on rõhukõikumisega adsorptsiooniga lämmastiku tootmine eriti sobiv vahelduva töö jaoks.
Seni on aga kodumaised ja välismaised kolleegid PSA lämmastiku tootmistehnoloogia abil toota ainult 99,9% puhtusega (st O2≤0,1%) lämmastikku. Mõned ettevõtted suudavad toota 99,99% puhast lämmastikku (O2≤0,01%). PSA lämmastiku tootmistehnoloogia seisukohast on võimalik kõrgem puhtusaste, kuid tootmiskulud on liiga kõrged ja kasutajad seda tõenäoliselt ei aktsepteeri. Seetõttu peab PSA lämmastiku tootmistehnoloogia kasutamine kõrge puhtusastmega lämmastiku tootmiseks lisama ka etapijärgse puhastusseadme.
Lämmastiku puhastamise meetod (tööstuslikus mastaabis)
(1) Hüdrogeenimise deoksügeenimise meetod.
Katalüsaatori toimel reageerib lämmastiku jääkhapnik lisatud vesinikuga ja tekib vesi ja reaktsiooni valem on: 2H2 + O2 = 2H2O. Seejärel eemaldatakse vesi kõrgsurve lämmastikukompressori võimendiga ja kõrge puhtusastmega lämmastik järgmiste põhikomponentidega saadakse järelkuivatamise teel: N2≥99,999%, O2≤5×10-6, H2≤1500× 10-6, H2O≤10,7×10-6. Lämmastiku tootmise maksumus on umbes 0,5 jüaani/m3.
(2) Hüdrogeenimise ja hapniku eemaldamise meetod.
See meetod jaguneb kolmeks etapiks: esimene etapp on hüdrogeenimine ja hapniku eemaldamine, teine etapp on dehüdrogeenimine ja kolmas etapp on vee eemaldamine. Saadakse kõrge puhtusastmega lämmastik järgmise koostisega: N2 ≥ 99,999%, O2 ≤ 5 × 10-6, H2 ≤ 5 × 10-6, H2O ≤ 10,7 × 10-6. Lämmastiku tootmise maksumus on umbes 0,6 jüaani/m3.
(3) Süsiniku desoksügeenimise meetod.
Süsiniktoega katalüsaatori toimel (teatud temperatuuril) reageerib tavalises lämmastikus olev jääkhapnik süsinikuga, mille katalüsaator ise annab, tekitades CO2. Reaktsiooni valem: C + O2 = CO2. Pärast järgnevat CO2 ja H2O eemaldamise etappi saadakse kõrge puhtusastmega lämmastik järgmise koostisega: N2 ≥ 99,999%, O2 ≤ 5 × 10-6, CO2 ≤ 5 × 10-6, H2O ≤ 10,7 × 10-6. Lämmastiku tootmise maksumus on umbes 0,6 jüaani/m3.
Kolmandaks: membraanide eraldamine ja õhu eraldamine lämmastiku tootmine
Membraani eraldamine ja õhu eraldamine lämmastiku tootmine on ka mittekrüogeense lämmastiku tootmistehnoloogia uus haru. Tegemist on uue lämmastiku tootmismeetodiga, mis arenes kiiresti välja 1980. aastatel välismaal. Seda on viimastel aastatel Hiinas propageeritud ja rakendatud.
Membraani eraldamise lämmastiku tootmisel kasutatakse toorainena õhku. Teatud rõhu all kasutab see õõneskiudmembraanis hapniku ja lämmastiku erinevat läbitungimise kiirust, et eraldada hapnik ja lämmastik lämmastiku tootmiseks. Võrreldes ülaltoodud kahe lämmastiku tootmismeetodiga on sellel lihtsam seadmete struktuur, väiksem maht, lülitusklapi puudumine, lihtsam töö ja hooldus, kiirem gaasi tootmine (3 minuti jooksul) ja mugavam võimsuse laiendamine.
Õõneskiudmembraanidel on aga suruõhu puhtusele rangemad nõuded. Membraanid on altid vananemisele ja purunemisele ning neid on raske parandada. Uued membraanid tuleb välja vahetada.
Membraani eraldamise lämmastiku tootmine sobib rohkem väikestele ja keskmise suurusega kasutajatele, kelle lämmastiku puhtusnõuded on ≤98%, ning sellel on praegu parim funktsiooni ja hinna suhe; kui lämmastiku puhtus peab olema kõrgem kui 98%, on see umbes 30% kõrgem kui sama spetsifikatsiooniga rõhukõikumisega adsorptsiooniga lämmastiku tootmisseade. Seega, kui kõrge puhtusastmega lämmastikku toodetakse membraanide eraldamise lämmastiku tootmise ja lämmastiku puhastusseadmete kombineerimisel, on üldise lämmastiku puhtus üldiselt 98%, mis suurendab puhastusseadme tootmiskulusid ja töökulusid.
Postitusaeg: 24. juuli 2024