Xinfa keevitusseadmetel on kõrge kvaliteedi ja madala hinnaga omadused. Üksikasjade saamiseks külastage:Keevitus- ja lõikamisseadmete tootjad – Hiina keevitus- ja lõiketehas ning tarnijad (xinfatools.com)
4. Kaare šahtid
Tegemist on allapoole libiseva nähtusega keevisõmbluse lõpus, mis mitte ainult ei nõrgenda keevisõmbluse tugevust, vaid põhjustab jahutusprotsessi käigus ka pragusid.
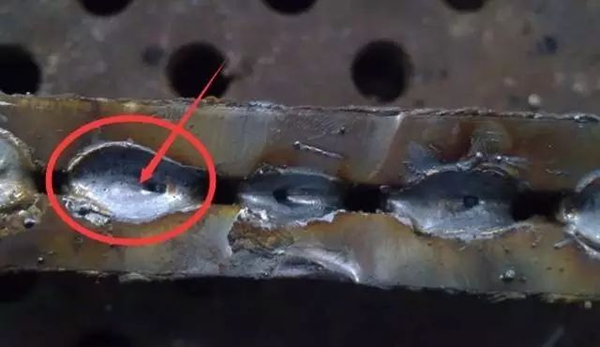
4.1 Põhjused:
Peamiselt on kaare kustutusaeg keevitamise lõpus liiga lühike või õhukeste plaatide keevitamisel kasutatav vool liiga suur.
4.2 Ennetavad meetmed:
Kui keevisõmblus on lõppenud, pange elektrood lühikeseks ajaks seisma või tehke mitu ringikujulist liigutust. Ärge peatage kaar järsult, et sulabasseini täitmiseks oleks piisavalt metalli. Tagada keevitamise ajal sobiv vool. Põhikomponendid saab varustada kaarekäivitusplaatidega, et juhtida kaare süvend keevisõmblusest välja.
5. Räbu kaasamine
5.1 Nähtus: mittepurustavate katsete käigus leitakse keevisõmbluses mittemetallilisi lisandeid, nagu oksiidid, nitriidid, sulfiidid, fosfiidid jne, mis moodustavad mitmesuguseid ebakorrapäraseid kujundeid ning tavalised on koonusekujulised, nõelakujulised ja muud räbu kandmisel. Metallkeevisõmblustes sisalduv räbu vähendab metallkonstruktsioonide plastilisust ja tugevust ning suurendab ka pinget, mille tulemuseks on külma ja kuuma rabedus, mida on lihtne puruneda ja komponente kahjustada.
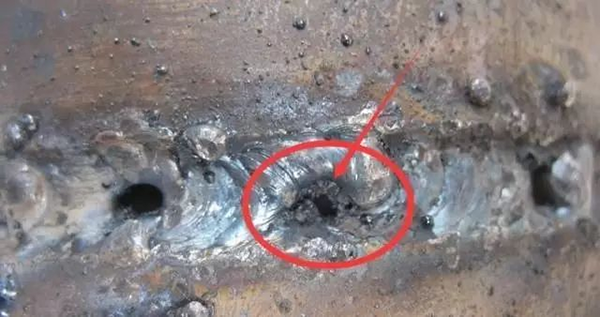
5.2 Põhjused:
5.2.1 Keevisõmbluse mitteväärismetall pole korralikult puhastatud, keevitusvool on liiga väike, sulametall tahkub liiga kiiresti ja räbu ei jõua välja ujuda.
5.2.2 Keevitusväärismetalli ja keevitusvarda keemiline koostis on ebapuhas. Kui keevitamise ajal on sulabasseinis mitu komponenti, nagu hapnik, lämmastik, väävel, fosfor, räni jne, tekivad kergesti mittemetallilised räbu lisandid.
5.2.3 Keevitaja ei ole tööks kvalifitseeritud ja varda transpordimeetod on vale, mistõttu räbu ja sularaud on segunenud ja lahutamatud, mis takistab räbu hõljumist.
5.2.4 Keevissoone nurk on väike, keevisvarda kate pudeneb tükkidena maha ja kaar ei sula; mitmekihilise keevitamise ajal ei puhastata räbu korralikult ja räbu ei eemaldata töö ajal õigeaegselt, mis on kõik räbu kaasamise põhjused.
5.3 Ennetus- ja tõrjemeetmed
5.3.1 Kasutage ainult hea keevitusprotsessiga keevitusvardaid ja keevitatud teras peab vastama projekteerimisdokumentide nõuetele.
5.3.2 Valige keevitusprotsessi hindamise kaudu mõistlikud keevitusprotsessi parameetrid. Pöörake tähelepanu keevissoone ja servapiirkonna puhastamisele. Keevitusvarda soon ei tohiks olla liiga väike. Mitmekihiliste keevisõmbluste puhul tuleb iga keevisõmbluse kihi keevitusräbu hoolikalt eemaldada.
5.3.3 Happeliste elektroodide kasutamisel peab räbu jääma sulabasseini taha; vertikaalsete nurkõmbluste keevitamiseks leeliselektroodide kasutamisel tuleb lisaks keevitusvoolu õigele valikule kasutada ka lühikaarkeevitust. Samal ajal tuleks elektroodi õigesti liigutada, et elektrood korralikult kõikuks, nii et räbu pinnale ujuks.
5.3.4 Kasutage eelsoojendust enne keevitamist, kuumutamist keevitamise ajal ja isolatsiooni pärast keevitamist, et jahutada aeglaselt, et vähendada räbu lisamist.
6. Poorsus
6.1 Nähtus: Keevitusprotsessi käigus sulanud keevismetallis neeldunud gaas ei jõua enne jahutamist sulavannist välja voolata ja jääb keevisõmbluse sisse auke moodustama. Pooride asukoha järgi võib need jagada sise- ja välispoorideks; Vastavalt pooride defektide jaotusele ja kujule vähendab pooride olemasolu keevisõmbluses keevisõmbluse tugevust ja tekitab ka pingekontsentratsiooni, suurendab madala temperatuuri haprust, termilist pragunemist jne.
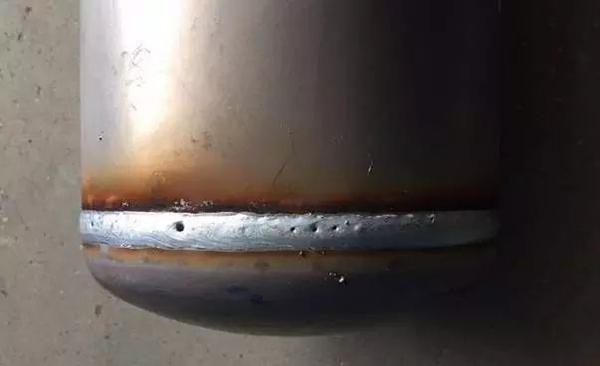
6.2 Põhjused
6.2.1 Keevitusvarda enda kvaliteet on halb, keevitusvarras on niiske ega kuivatatud vastavalt etteantud nõuetele; keevisvarda kate on rikutud või maha koorunud; keevissüdamik on roostetanud jne.
6.2.2 Lähtematerjali sulatamisel on jääkgaasi; keevitusvarras ja keevisõmblus on määrdunud lisanditega nagu rooste ja õli ning keevitusprotsessi käigus tekib kõrge temperatuuriga gaasistamise tõttu gaas.
6.2.3 Keevitaja ei ole kogenud töötehnoloogiat või tal on halb nägemine ja ta ei suuda eristada sularauda ja kattekihti, mistõttu kattes olev gaas seguneb metallilahusega. Keevitusvool on liiga suur, muutes keevitusvarda punaseks ja vähendades kaitseefekti; kaare pikkus on liiga pikk; toitepinge kõigub liiga palju, mistõttu kaar põleb ebastabiilselt jne.
6.3 Ennetus- ja tõrjemeetmed
6.3.1 Valige kvalifitseeritud keevitusvardad ja ärge kasutage mõranenud, koorunud, kulunud, ekstsentrilise või tugevalt roostetanud kattega keevitusvardaid. Puhastage õliplekid ja roosteplekid keevisõmbluse lähedal ja keevitusvarda pinnal.
6.3.2 Valige sobiv vool ja reguleerige keevituskiirust. Enne keevitamist soojendage töödeldavat detaili. Kui keevitamine on lõppenud või peatatud, tuleb kaar aeglaselt välja tõmmata, mis aitab aeglustada sulabasseini jahutuskiirust ja gaasi väljutamist sulabasseinis, vältides pooride defektide tekkimist.
6.3.3 Vähendage keevituskoha niiskust ja tõstke töökeskkonna temperatuuri. Õues keevitamisel, kui tuule kiirus ulatub 8 m/s, vihm, kaste, lumi jne, tuleks enne keevitamist rakendada tõhusaid meetmeid, nagu tuuletõkked ja varikatused.
7. Pritsmete ja keevitusräbu puhastamata jätmine pärast keevitamist
7.1 Fenomen: see on kõige levinum probleem, mis pole mitte ainult inetu, vaid ka väga kahjulik. Sulavad pritsmed suurendavad materjali pinna kõvastunud struktuuri ja on lihtne tekitada selliseid defekte nagu kõvenemine ja lokaalne korrosioon.
7.2 Põhjused
7.2.1 Keevitusmaterjali ravimkate on ladustamise ajal niiske ja rikutud või valitud keevitusvarras ei vasta lähtematerjalile.
7.2.2 Keevitusseadmete valik ei vasta nõuetele, vahelduv- ja alalisvoolu keevitusseadmed ei sobi keevitusmaterjalidega, keevitusliini polaarsusühendusviis on vale, keevitusvool on suur, keevissoone serv on on saastunud prahi ja õliplekkidega ning keevituskeskkond ei vasta keevitusnõuetele.
7.2.3 Operaator ei ole kvalifitseeritud ning ei tööta ega kaitse eeskirjade kohaselt.
7.3 Ennetus- ja tõrjemeetmed
7.3.1 Valige sobiv keevitusseade vastavalt keevitusmaterjalile.
7.3.2 Keevitusvardal peab olema kuivatus- ja püsitemperatuuri varustus ning kuivatusruumis peab olema õhukuivati ja konditsioneer, mis ei asu maapinnast ja seinast vähem kui 300mm. Luua süsteem keevitusvarraste vastuvõtmiseks, saatmiseks, kasutamiseks ja hoidmiseks (eriti surveanumate puhul).
7.3.3 Puhastage keevisõmbluse serv, et eemaldada prahist niiskus, õliplekid ja rooste. Talvisel vihmaperioodil ehitatakse keevituskeskkonna tagamiseks kaitsekuur.
7.3.4 Enne värviliste metallide ja roostevaba terase keevitamist võib mõlemale poolele keevisõmbluse lähtematerjalidele kanda kaitsekatted. Pritsmete kõrvaldamiseks ja räbu vähendamiseks saate valida ka keevitusvardad, õhukese kattega keevitusvardad ja argoonikaitse.
7.3.5 Keevitus nõuab õigeaegset keevitusräbu puhastamist ja kaitset.
8. Kaare arm
8.1 Nähtus: Hooletu kasutamise tõttu puutub keevisvarras või keevituskäepide kokku keevisõmblusega või maandusjuhe puutub töödeldava detailiga halvasti, tekitades lühiajaliselt kaare, jättes tooriku pinnale kaarearmi.
8.2 Põhjus: Elektrikeevitusoperaator on hooletu ega võta kasutusele kaitsemeetmeid ega hoolda tööriistu.
8.3 Ennetavad meetmed: Keevitajad peaksid regulaarselt kontrollima kasutatud keevituskäepideme juhtme ja maandusjuhtme isolatsiooni ning vigastuste korral need õigeaegselt pakkima. Maandusjuhe tuleb paigaldada kindlalt ja usaldusväärselt. Ärge käivitage keevitamisel kaar väljaspool keevisõmblust. Keevitusklamber tuleb asetada lähtematerjalist eraldi või sobivalt riputada. Katkesta toiteallikas õigeaegselt, kui te ei keevita. Kaarkriimude leidmisel tuleb need õigeaegselt elektrilise lihvkettaga poleerida. Kuna toorikutel, millele kehtivad korrosioonikindluse nõuded, nagu roostevaba teras, saavad kaarearmid korrosiooni alguspunktiks ja vähendavad materjali jõudlust.
9. Keevisarmid
9.1 Nähtus: Keevitusarmide mittepuhastamine pärast keevitamist mõjutab seadme makroskoopilist kvaliteeti ning ebaõige käsitsemine põhjustab ka pinnapragusid.
9.2 Põhjus: Mittestandardsete seadmete tootmisel ja paigaldamisel tekivad positsioneerivad keevitusseadmed, kui need pärast valmimist eemaldatakse.
9.3 Ennetavad meetmed: montaažiprotsessis kasutatavad tõsteseadmed tuleb lihvkettaga poleerida, et need oleksid pärast eemaldamist algmaterjaliga tasapinnalised. Alusmaterjali kahjustamise vältimiseks ärge kasutage kinnituste maha löömiseks haamrit. Elektrikeevitamise ajal liiga sügavad kaareaugud ja kriimustused tuleks parandada ja lihvkettaga poleerida, et need oleksid algmaterjaliga tasapinnalised. Kui olete töö ajal tähelepanelik, saab selle defekti kõrvaldada.
10. Mittetäielik läbitungimine
10.1 Nähtus: Keevitamise ajal ei ole keevisõmbluse juur põhimaterjaliga täielikult kokku sulanud või on lähtematerjal ja lähtematerjal osaliselt mittetäielikult keevitatud. Seda defekti nimetatakse mittetäielikuks läbitungimiseks või mittetäielikuks sulandumiseks. See vähendab vuugi mehaanilisi omadusi ja põhjustab selles piirkonnas pinge kontsentratsiooni ja pragusid. Keevitamisel ei tohi ühegi keevisõmbluse läbitungimine olla mittetäielik.
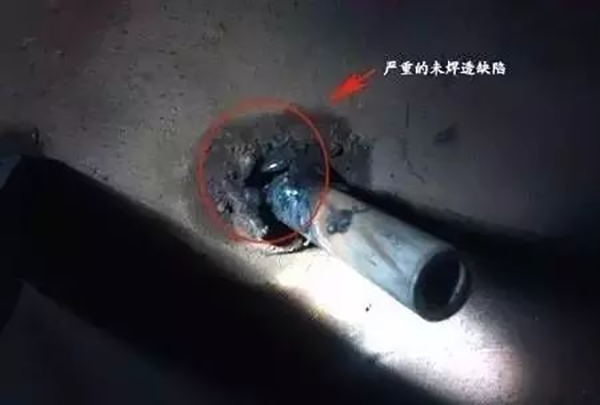
10.2 Põhjused
10.2.1 Soon ei ole eeskirjade kohaselt töödeldud, tömbi serva paksus on liiga suur ja soone nurk või koostu vahe on liiga väike.
10.2.2 Kahepoolsel keevitamisel ei puhastata põhjalikult tagumist juurt või ei puhastata soone külgi ja kihtidevahelist keevisõmblust, mistõttu oksiidid, räbu jms takistavad metallide vahelist täielikku sulandumist.
10.2.3 Keevitajal puudub tööoskus. Näiteks kui keevitusvool on liiga suur, ei ole alusmaterjal sulanud, kuid keevitusvarras on sulanud, nii et alusmaterjal ja keevitusvarda ladestatud metall ei ole kokku sulanud; kui vool on liiga väike; keevitusvarda kiirus on liiga suur, alusmaterjali ja keevitusvarda ladestatud metalli ei saa hästi sulatada; töös on keevitusvarda nurk vale, sulamine on ühele poole kaldu või tekib keevitamise ajal puhumine, mis põhjustab mittetäieliku läbitungimise kohtades, kus kaar ei saa toimida.
10.3 Ennetavad meetmed
10.3.1 Töötle ja monteeri vahe vastavalt projektjoonises või spetsifikatsioonistandardis määratud soone suurusele.
Postitusaeg: 28. juuli 2024